5G-La concept of the district of Uelzen5G in agriculture
Finanziell gefördert durch
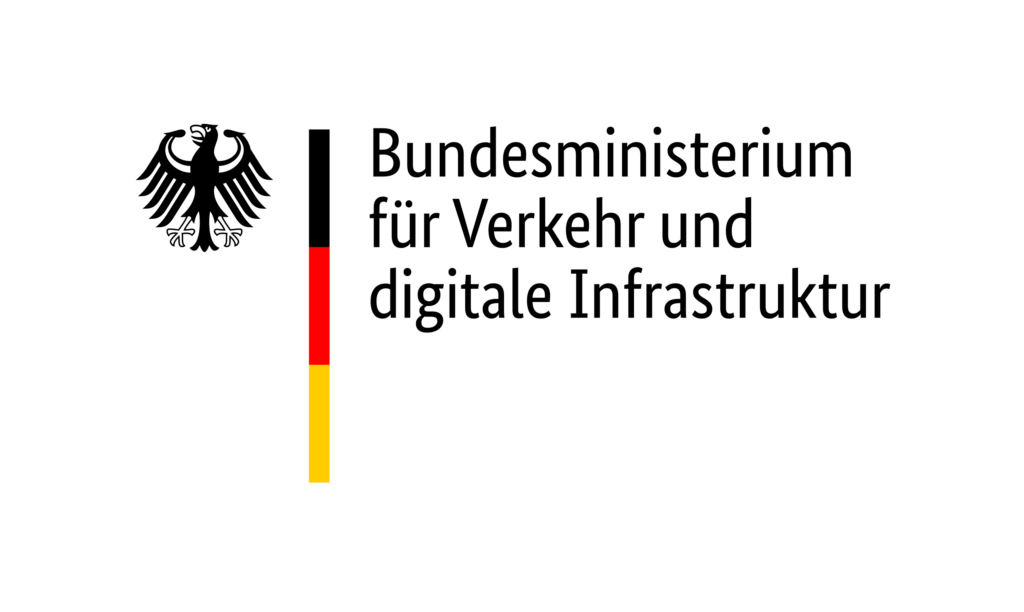
Projectpartner
Project Homepage
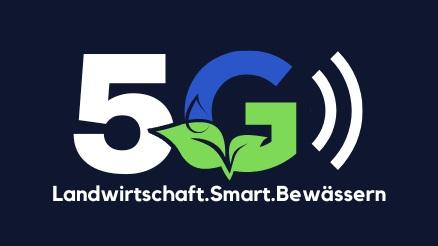
Water is the most important production factor in agriculture worldwide and therefore in the production of food. Additional irrigation is necessary in unfavorable soil or climatic conditions, to safeguard and increase productivity in an environmentally friendly manner or to grow higher-value products.
The overall system of field irrigation must be further developed in order to achieve the efficient use of water as a production factor (water quantity requirement, use of resources for implementation, costs of irrigation) with the best possible field yields. It is necessary to consider the system as a whole, as progress in one aspect alone brings little or no improvement in results.
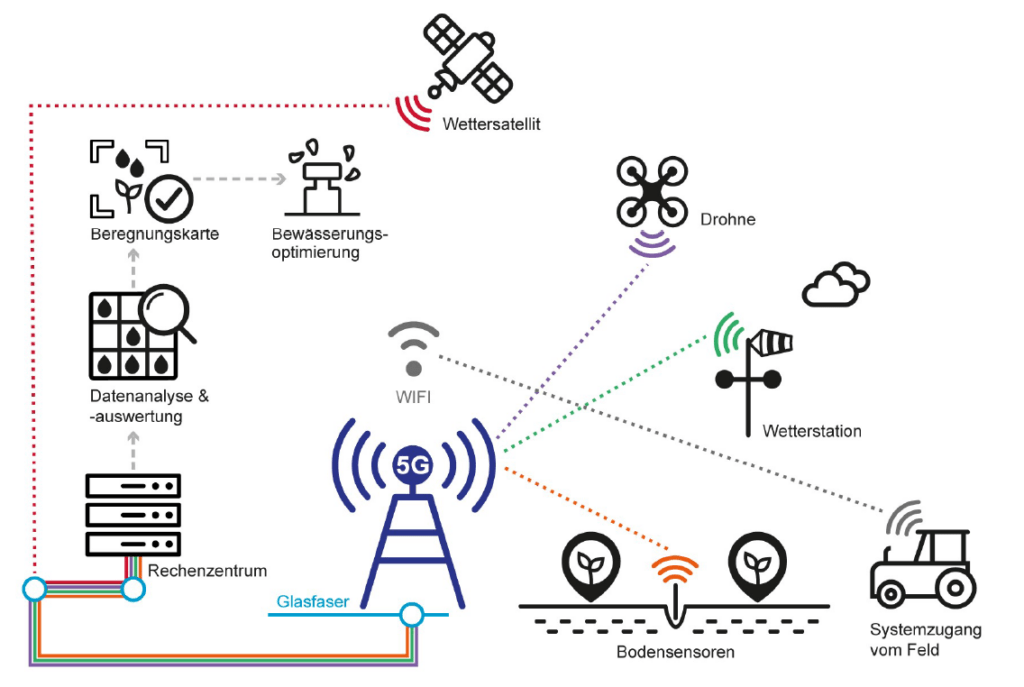
The aim of this concept is to determine the basis for irrigation optimization through the use of a 5G experimental field. These serve to evaluate and develop a future overall “field irrigation” system consisting of sensors, actuators, data management, evidence-based decision-making and implementation control. In direct application, 5G technology is used to work on technical solutions for determining the water status of the cultivated area, soil properties and plant status. Sensors and sensor platforms as well as the necessary data processing procedures (analysis, databases, interfaces, etc.) are being developed. The aim is to achieve suitability for everyday use and marketable applications.
Test year 2023
In the current test phase, soil moisture sensors from six different manufacturers are being compared with each other in laboratory and field tests. The sensors will transmit the measurement results to the data center/data platform via 5G.
Structure of the laboratory tests at INBW
The laboratory tests were planned and set up at INBW at the beginning of the year in order to test soil moisture sensors. The main objective was to test the sensors under different scenarios in parallel.
in parallel. In addition, the test setup was developed so that sensors from different manufacturers (which use different measurement methods) could be tested and compared for their functionality.
The test facility comprises a filled reactor with a defined base and a drainage layer. This drainage layer consists of 16/32 mm gravel covered with a geotextile.
The reactors are uniformly filled with slightly silty sand (Su2). The measuring depth of the sensors varies between 55 cm and 105 cm depending on the reactor type. Each reactor is equipped with a plant lamp to simulate daylight. This enables tests under laboratory conditions with limited light conditions for sensors that charge their battery with solar cells. In addition, this equipment allows the simulation of other scenarios in which light plays a decisive role. For example, tests with catch crops, etc.
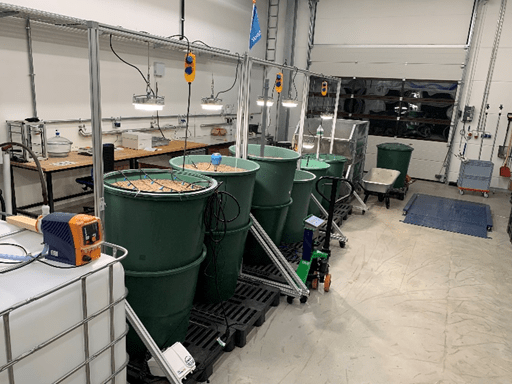
Mobile transmitter mast
A 30 meter high mobile phone mast was erected as part of the project. The agricultural test area to be made accessible by radio technology is 1.4 km². In addition, a data center was set up both on the test field and on the AGRAVIS Future Farm test farm. These technical components have been connected to the fiber optic network to ensure data exchange. The selected mast was erected on 27.02.2023. The maximum construction height is 30 m and the total weight is 9 tons. Due to the installation height, the trees in the immediate vicinity can be towered over (see Fig. 4 to 6). The mast includes an attached technical container with a pneumatically extendable aluminum mast. The area (8×8 m) is provided with protective fencing.
Start of field investigations
Sampling of trial field 1 took place from March to April 2023. Comprehensive soil tests were carried out at selected measuring points in the field. The picture shows a schematic of the equipment used to create a small trench as well as the soil sampling cylinders used to take soil samples with as little disturbance as possible. This enables the analysis
the field capacity of a soil body in the laboratory.
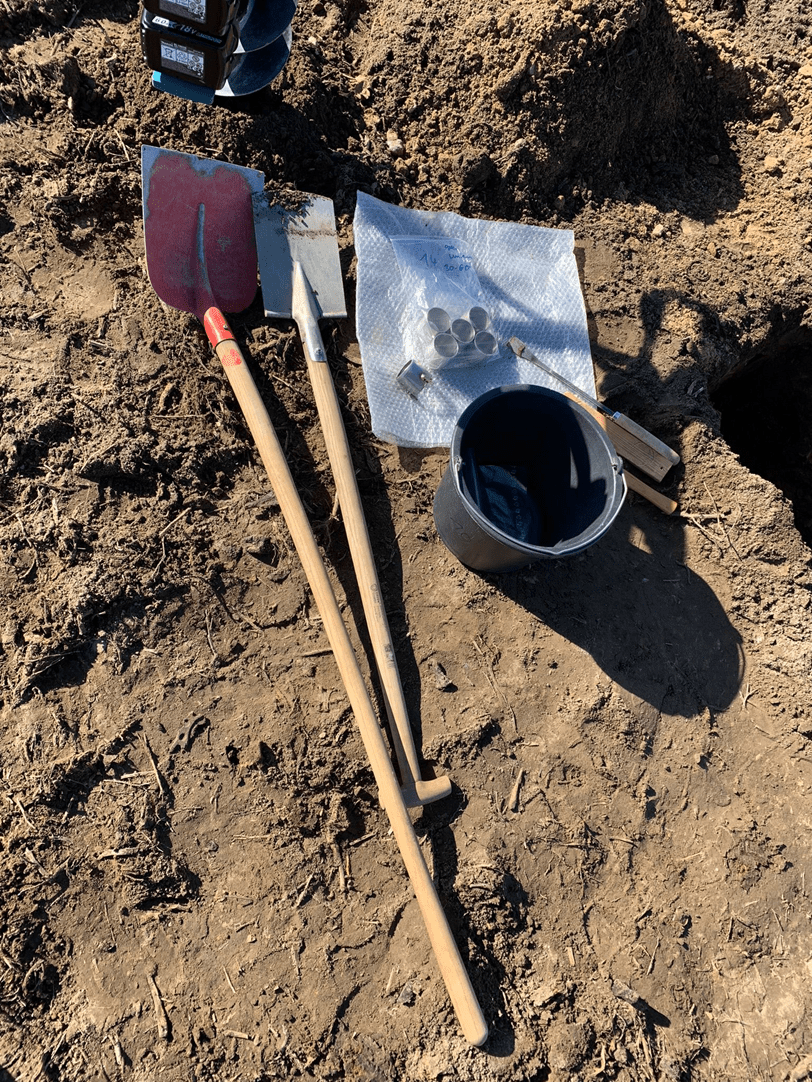
The following figure shows soil samples taken from different horizons, which are used in the Ostfalia laboratory to determine the gravimetric water content. The first measurement campaign was carried out in the summer of 2023 to check the accuracy of the sensors for the 5G project. Various depths in the soil profile were analyzed.
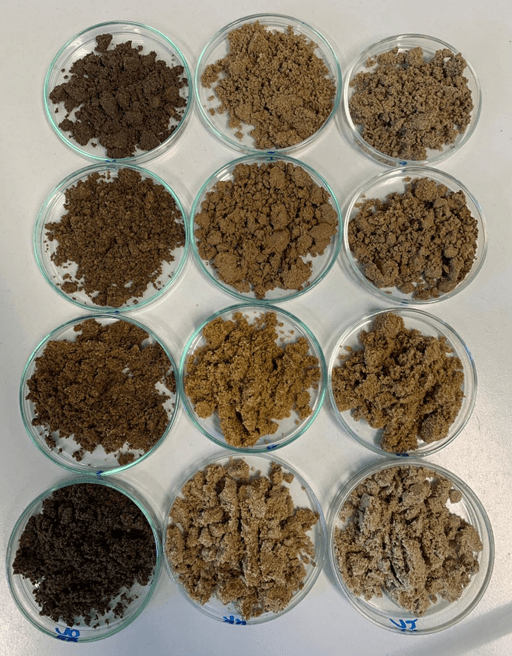
Photo gallery of installed sensors in test field 1
The first trial period in the field lasted from 04.05.2023 (installation of the sensors) to 21.09.2023. Schematic photo: The sensors were removed from the “Rampe” field on 21.09.2023. After checking the sensors and siccating the potatoes, the various sensors were removed from the “Rampe” field. This was followed by a recommendation on how to proceed with soil moisture sensors
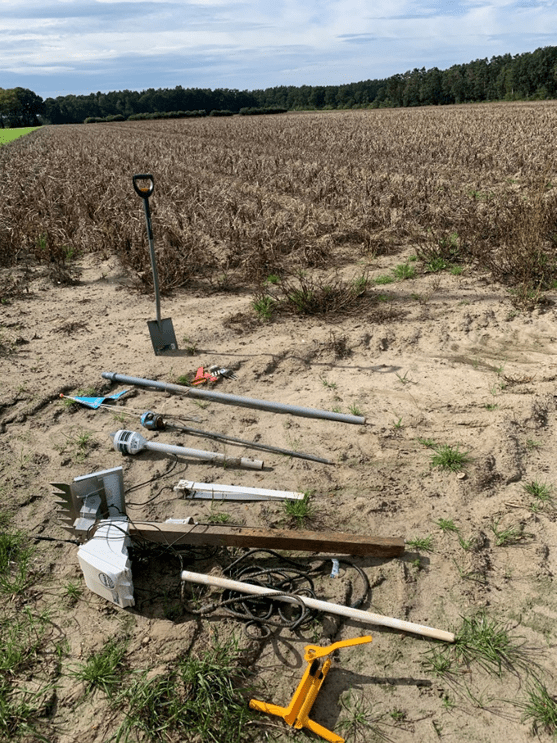
(Schmidt, 2023)
On 17.10.2023, additional sensors (Sentek Drill & Drop sensors) were installed on the “Meyer field barn” plot. This serves to gain additional knowledge about the catch crop (ZF) over the course of the winter half-year and to examine its water requirements in more detail.
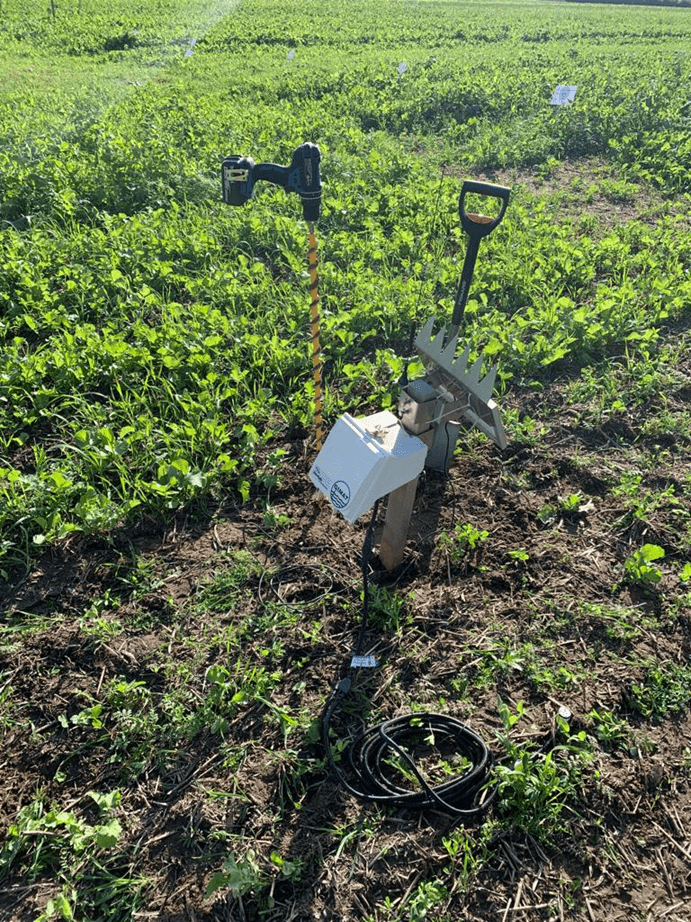
Soil samples were taken from the current test area in order to adjust the soil moisture probes to be tested. The soil samples taken were examined in the soil laboratory at Ostfalia University in Suderburg.
Drone overflights
At the same time as installing the sensors, Domenik Jentsch carries out a flyover of the “Meyer field barn” parcel. A DJI Matrice 210 equipped with a multispectral camera (RedEdge P Dual) is used for this. The flight altitude is a constant 100 m above the parcel and the speed is between 8 and 10 m/s (rounded). The actual flight time is about 15 minutes, while the preparation and post-processing of the drone takes about 5 minutes. The drone flies semi-autonomously. Approximately 260 multispectral images are taken during the flight. This image data will be transmitted via 5G as the project progresses. After the flyover, the individual images are merged into an orthophoto using Agisoft Metashape. Various indexes can then be calculated on this. These can be used to obtain various information regarding plant growth, health, etc.
Subsequently, images are taken with infrared, multispectral and RGB camera systems and merged into an orthophoto
Status November 2023:
The test facility developed at INBW is being expanded to detect soil moisture with the help of a multispectral camera (MicaSense RedEdge MX). For this purpose, the multispectral camera is permanently installed above the garbage cans. The images are also transmitted via the 5G campus network. This step therefore also serves as a test under ideal conditions (camera stationary, full signal strength) for
the 5G transmission. If this step is successfully implemented, the automated process can then be used in real field conditions. In the field, the drone is equipped with a mini PC with a 5G transmitter unit to send the images to the data platform during flight.
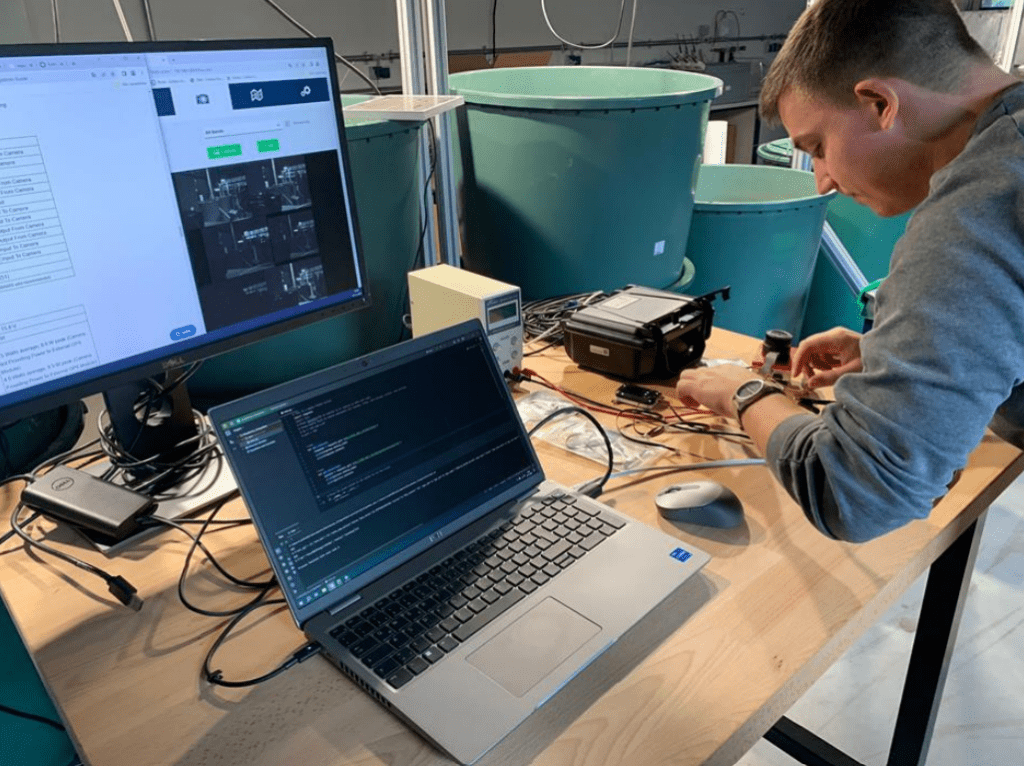
Project manager
Nathalie Kockemüller M.Sc
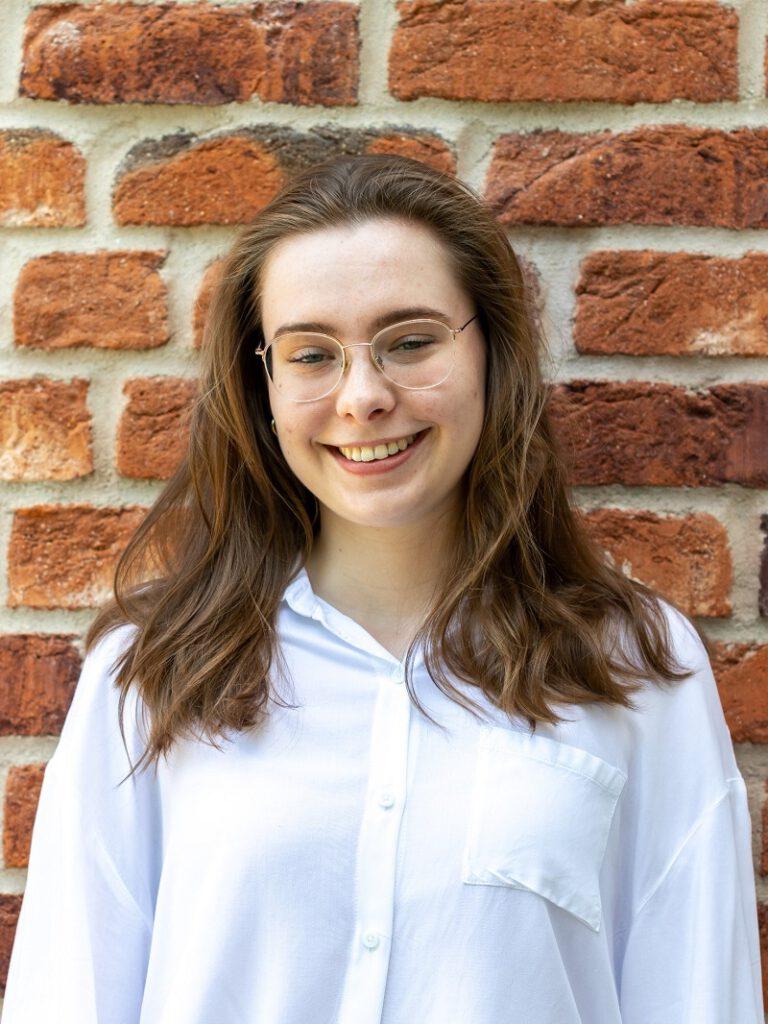
Email: | na.kockemueller@ostfalia.de |
Phone: | +49 5826 988 61620 |
IT specialist
Domenik Jentsch, B.Sc.
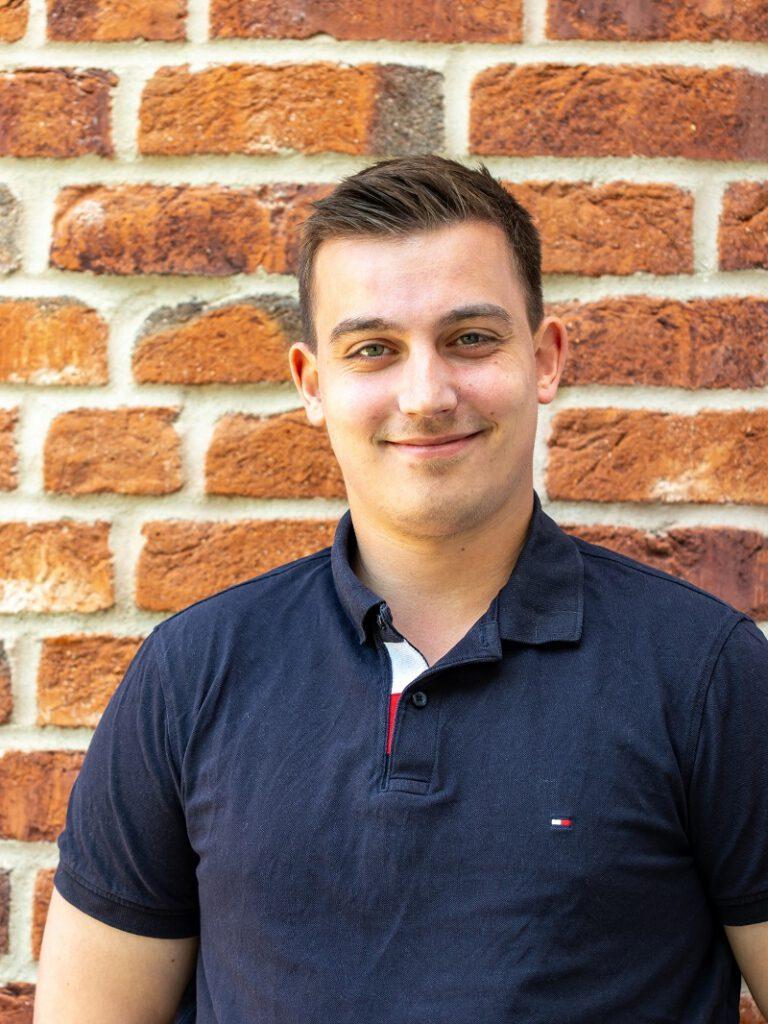
Email: | dom.jentsch@ostfalia.de |
Phone: | +49 5826 988 61500 |
Testing and measurement
Felix Schmidt M.Sc.
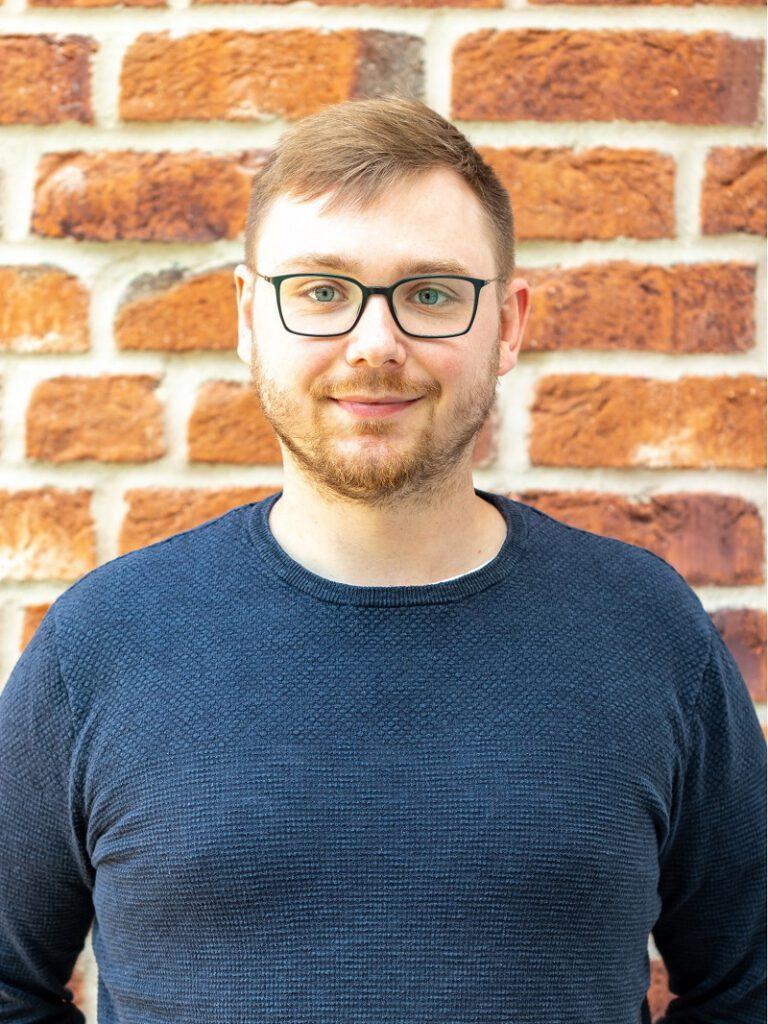
Email: | felix.schmidt@ostfalia.de |
Phone: | +49 5826 988 61580 |
Project manager:
Prof. Dr.-Ing. Klaus Röttcher
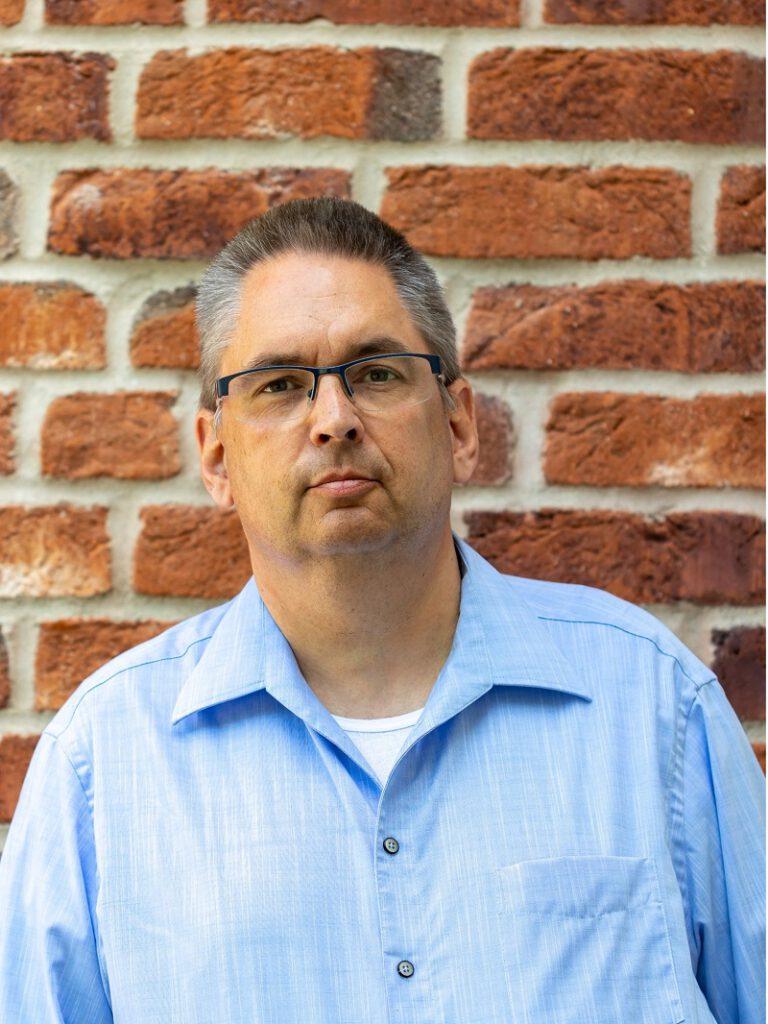
Email: | k.roettcher@ostfalia.de |
Phone: | +49 5826 988 61230 |